Foam ceramic filter
• Foam ceramic filter generally uses polyurethane ethyl foam as the carrier, filled with a ceramic slurry made of refractory aggregate sintering additives, binders and other micro powders and water, and then extrudes the slurry, leaving the ceramic material wrapped around the foam fiber, which is dried and roasted and sintered at high temperature, and the polyurethane is decomposed by heat, leaving a foam-like ceramic product, that is, a foam ceramic filter
• Ceramic materials used for molten metal filtration have a very high melting point and do not melt during casting nor decompose into molten metal.
2. Specifications of the filter
• The number in front of the PPI represents the pore density of the product. If the model is 10ppi, it means that the pore uniformity on any 25.4mm length is 8-12
Generally, 10ppi is used for casting ductile iron, 10/20ppi for gray iron, 20/25ppi for cast aluminum, and 25/30ppi for cast copper according to the cleanliness of the solution. However, it still needs to be judged based on actual usage. Foam filter plate products with holes.
Filtration mechanism of ceramic filters
•Screening. Like a sieve, it prevents the passage of inclusions and their agglomerates that are larger than the pore size of the filter surface.
• Crepe filter. After screening, many inclusions larger than the filter pores are trapped at the filter inlet. As the number of captured inclusions increases, a "filter cake" consisting of large inclusions is formed on the surface of the filter inlet. The "filter cake" makes the liquid thinner, so that inclusions smaller than the filter pore size are also partially trapped on the "filter cake".
• Deep bed filtration. In the foam ceramic filter, the path through which the melt flows is meandering, and there is even a phenomenon of cross-flow reentry in a small local area, which mainly plays two roles: (1) it can greatly increase the probability of contact between the inclusion particles and the filter; (2) The flow velocity and flow direction of the melt are accelerated, so that the fine inclusions in the melt can be trapped after being left in a certain corner after the collision.
Straight bore filter slag retaining (screening) Ceramic foam filter slag retaining (sifting)
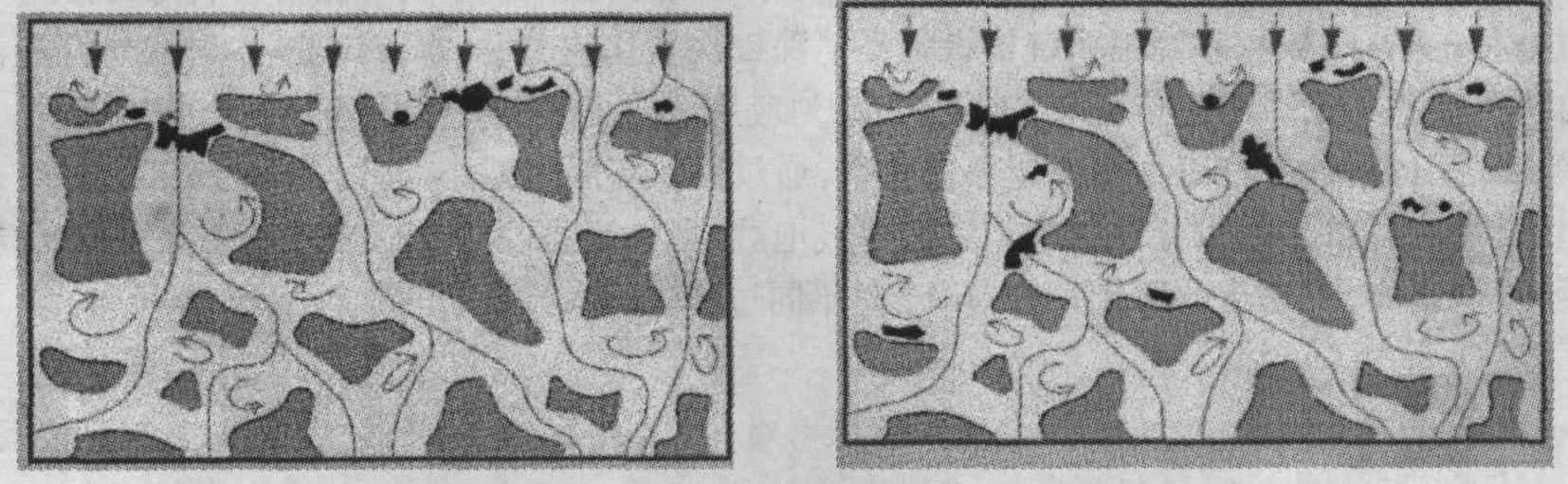
Filter cake and depth filter bed for foam ceramic filter
The function of the ceramic foam filter• Slag removal: purification of molten metal and degassing at the same time (adjustment of turbulence):
- After filtration, the viscosity of the molten metal solution decreases, and the fluidity of the aluminum alloy liquid increases by 10%-15%. Therefore, filtration improves the filling capacity of the molten metal.
--The flow of molten metal before filtration is turbulent, and after filtration, it becomes laminar flow (zigzag and bending in the flow channel of the foam ceramic filter), which reduces the coiling gas and secondary slag making;
--With the progress of filtration, the filtration mechanism changes from screening, filter cake to deep bed filtration, and the purity of the filtered molten metal is getting higher and higher (without exceeding the filtration capacity of the ceramic foam filter).
• Reduced scrap rate of parts,
• Improved cutting performance of parts
• Significant improvement in the mechanical properties of the material, especially the elongation.
S
election of filter size•Step 1: Calculate the minimum cross-sectional area of the sprue
• Step 2: Calculate the sum of the cross-sectional areas of the cross sprue and the sum of the cross-sectional areas of the inner grace,
• Step 3: Determine the location and number of filters;
• Step 4: Determine the size of the filter according to the filtration speed of the filter per unit area, the filtration capacity of the filter per unit area, the actual pouring speed, the weight of the molten metal passing through the filter and the purity of the molten metal (if the molten metal is too impure, multi-stage filtration is required).
That is, the filtration speed of the filter> the pouring speed of the molten metal, the filtration capacity of the filter, > the amount of inclusions in the molten metal
• Usually: the filtration area of the filter is 2.5-4 times the cross-sectional area of the sprue.
Design of the gating system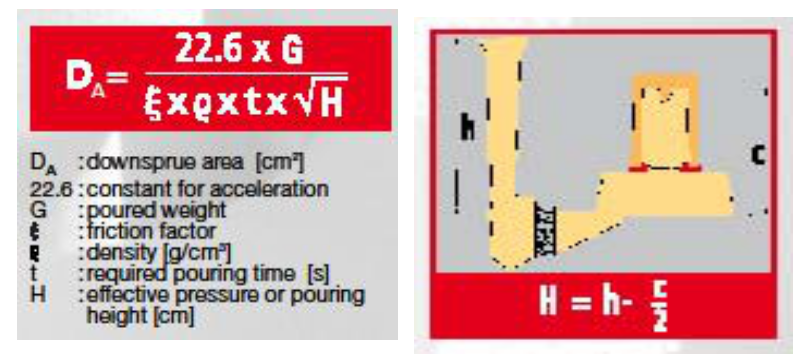
• DA: Sprue cross-section; 22.6: acceleration constant; G: Pouring weight;
• £: coefficient of friction; ρ: liquid density of aluminum alloy; pouring time; H: Effective pouring height
•S: Sprue cross-sectional area
•R: The total cross-sectional area of all sprues
•I: The total cross-sectional area of all sprues
•S:R:I=1.0:1.1:1.2
Selection of filter size• The area of the metal through the filter should be large enough, and the pouring speed and pouring time of the casting mold should not be affected because of the placement of the filter, so the factors of slag collection, filter and damping should be considered in the process, so the ratio of the area of the section at the filter to the normal sprue area is 2.5-4.0:1;
• There should be enough space before and after the filter to facilitate the collection of inclusions and the smooth flow of molten metal. In order to prevent filter inclusions from affecting the flow of metal, the filter size is selected according to the amount of molten metal filtration.
• If the whole package of molten metal is too much or too dirty, it can be split on the cross sprue and multiple filters can be used.
The design of the filter seat• Full consideration should be given to the ease of placement of the filter (such as cone, slope, gap, etc.) and firmness.
• The supporting surface of the mold should be rounded (plastered) to prevent sand washing.
Note that:--Leave 3-5mm lap on the molten metal inflow surface;
--The support width of >5mm should be left on the outflow surface of molten metal;
--There is a gap of 1.0-1.5mm and a sand collection groove around the filter to prevent the scattered sand particles from accidentally falling into the mold when inserting;
--The upper surface of the filter should be 0.5-1.0mm lower than the parting surface to prevent the filter from being crushed when closing the box (especially when there is sand on it).
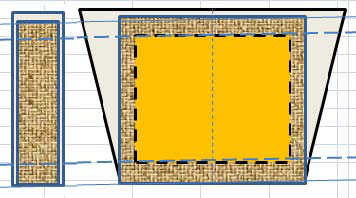
Place the slot filter in the filter area

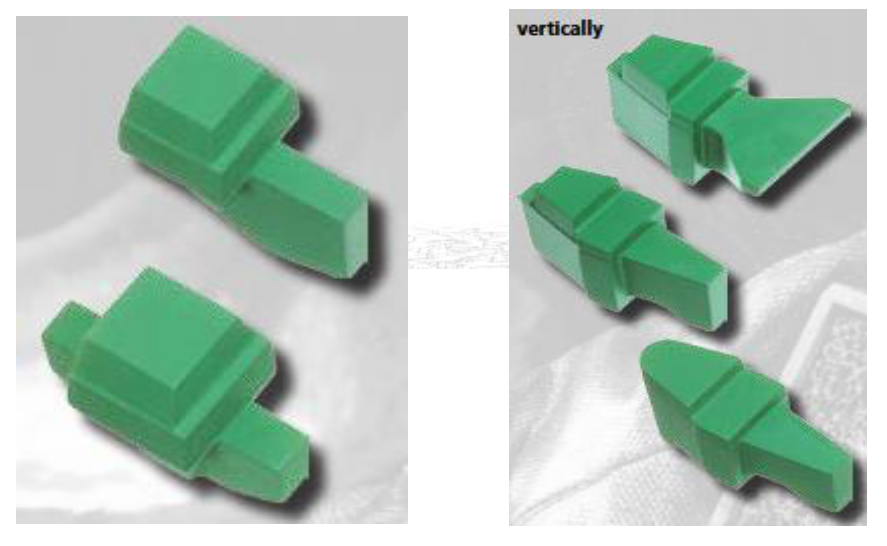
Common ways to place filters:
• The filter is placed horizontally, and the molten metal passes through the filter from the bottom up;
• Horizontal Placement:
--The utilization area of the filter is large;
--Top-down: In the initial stage of filtration, the filtered liquid flow has a shower phenomenon; As the liquid underneath fills up, the shower phenomenon disappears
--Bottom-up: Filtered liquid flow, no shower phenomenon
• Vertical Placement:
--At the beginning of filtration, the utilization area of the filter is small;
--There is no shower phenomenon in the filtered liquid flow
The state of the liquid flow before and after the filter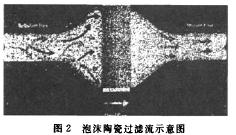
After the filter, the molten metal is in a laminar flow state
Precautions
• Improper use of ceramic filters, the effect is worse than the use of other filters;
• The system is designed to pass through the filter (if part of the molten metal does not pass, the molten aluminum will be impure, and turbulence will be generated, and the gas will be slag formed);
• The filtration area of the filter should be large enough not to affect the flow rate of the molten metal (the minimum flow rate should be located at the minimum section of the sprue);
• There should be enough space before and after the filter to facilitate the collection of inclusions.
• The metal melt should be smelted in the melting furnace (to avoid oxidation and slag removal) and the refining and slag removal and degassing in the holding furnace. Because the filter's filtration capacity is limited, the molten metal is too dirty, resulting in the filtered melt being dirtier than the filtered melt.
Notes:
• Ceramic filters should be baked and dried before use
• Debris on the ceramic filter should be blown off and should not be carried into the sprue.
• The ceramic filter should be placed correctly so that it does not crush.